Developing Safety Structures for Mobility as a Service vehicles
Steel E-Motive’s body structure design and specifications will deliver a steel-intensive Mobility as a Service vehicle, with features and attributes which are paramount for the introduction of a game-changing transportation mode. The vehicle is engineered around the user and fleet operator, placing a strong focus on Comfort and Convenience without compromising vehicle safety.
Steel E-Motive is designed to operate in a mixed traffic mode operation (both driver-operated and autonomous vehicles); hence the vehicle should meet the current and future global high-speed crash test standards. The compact vehicle dimensions and proportions result in relatively short front and rear overhangs. To enhance user experience and take advantage of full autonomy, the front occupants are positioned in a rear facing configuration presenting a more significant challenge for crashworthiness in frontal impact. This requires a revised front crash strategy and load management approach for Steel E-Motive. The high strength and formability properties of Advanced High-Strength Steels (AHSS) have enabled us to meet these unique and challenging requirements.
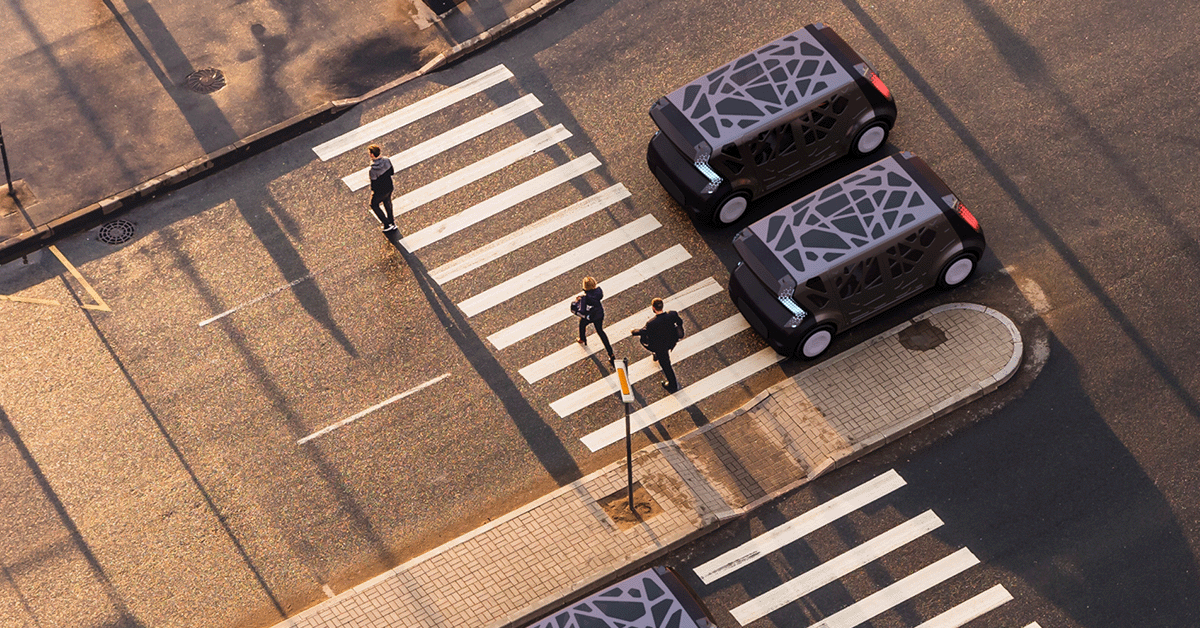
Front crash and protection in rear-facing configurations
One of the most challenging crash tests is the Insurance Institute for Highway Safety (IIHS) Small Offset Rigid Barrier overlap (SORB), which is a 64kph frontal impact into a rigid barrier connecting with 25% width of the vehicle. Different strategies for the crash load management and occupant protection can be applied for this test. One approach is to deflect or “glance” the vehicle away from the barrier following the impact. This results in lower vehicle kinetic (moving) energy being converted to impact (crush) energy, achieving reduced crash pulse (deceleration) and intrusion into the occupant space. To enable the vehicle to “glance” from the SORB barrier on impact, a very high-strength front corner structure is required, especially in the lateral (Y) direction. Alternatively, the crash load can be absorbed and managed using a conventional absorption approach, similar to Frontal Rigid Barrier (FFB) and Offset Deformable Barrier (ODB) tests. Here, the crash structure is engineered to decelerate the vehicle progressively and relies on a very high-strength hinge pillar and A-pillar structure to minimise intrusion to the cabin. Both strategies rely on attentive design of the body structure and appropriate selection of AHSS grades.
Vehicle front crash structures are also engineered for other crash test load cases such as the USNCAP Frontal Rigid Barrier (FFB) and Offset Deformable Barrier (ODB). Here, the aim is to fully absorb the impact energy in a controlled manor whilst minimising intrusion and injury to the occupant. The requirements of high-strength and rigidity elements for the SORB test and controlled crush absorption in the FFB and ODB tests can often conflict and therefore require careful design of the body front crash structure. The varied strength and ductility properties of AHSS’s enable engineers to balance the conflicting requirements of these front crash tests.
Within the Steel E-Motive project, specific crash intrusion targets for the IIHS SORB and ODB tests have been derived, deviating from conventional human operated vehicles. The existing test targets consider crash intrusion measurements for the driver interface positions such as “steering column” and “brake pedal”. For a Level 5 Autonomous vehicle, these targets are no longer applicable, and due to the rear facing position of the front occupant, additional intrusion measurement locations and targets are defined, specifically around the occupant head and torso region. These additional targets ensure that the risk of severe injury to the occupants in the event of a frontal collision are minimised.
The Steel E-Motive body structure incorporates several features to ensure the design meets the front crash worthiness requirements. The front bumper beam and crash longitudinals are optimised and oriented to engage with the SORB barrier on initial impact and initiate a high lateral force. The front subframe also plays an important role in stabilising the front structure and maintaining reaction forces to the SORB barrier. Extended upper rails (“SORB beams”) have been engineered to ensure the front structure maintains a sufficient lateral reaction force to guide the vehicle along the barrier, whilst not compromising the longitudinal crush requirement for the FFB and ODB tests. A high-strength shock tower and lateral brace ensure the vehicle maintains the glance trajectory and forms part of the intrusion prevention structure as the barrier nears the front occupants. The front hinge and A-pillars are fabricated from AHSS ensuring the structural integrity is maintained and intrusion values are minimised. Furthermore, the occupants are protected by an extended AHSS zone around the front header, cantrail and front bulkhead.
The USNCAP rigid barrier and IIHS ODB tests require a longitudinal crushable zone within the front crash rails. This results in a controlled and progressive collapse of the crash rail and protection of the occupants from high decelerations and intrusions.
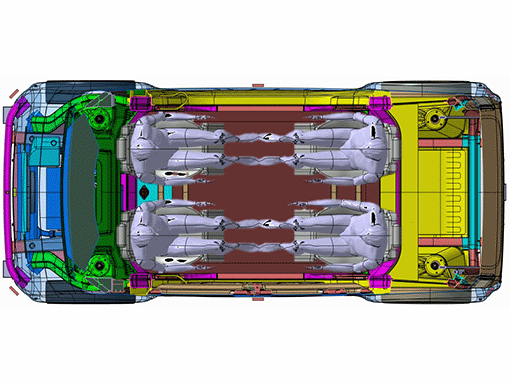
Autonomous vehicles present opportunities for new seating configurations. Steel E-Motive’s rear facing configuration presents a more significant challenge for crashworthiness in frontal impact requiring a revised front crash strategy and load management approach.
By implementing this strategy and the design features in the Steel E-Motive body, our vehicle concept achieves the desired crash worthiness targets, especially challenging with a unique occupant position and small front overhang. Here, AHSS properties enable fine tuning of the front crash structure in various locations for different requirements.
Side crash and battery protection
The main requirements for the side crash structure are the protection of occupants and the high voltage battery in the IIHS Moving Deformable Barrier and Euro NCAP Side Pole tests . The internal reinforcements of Steel E-Motive’s scissor door have been optimised to provide protection for the moving deformable barrier and compensate for the lack of a central B-pillar. For the standardized Side Pole test, the occupants are positioned inside of the AHSS A- and C-pillars near the pole impact zone, which provide very good protection. We also have considered more challenging side pole test locations along the length of the rocker, to ensure the high voltage battery structural integrity is maintained throughout. A crushable element has been engineered and optimised inside of the rocker to provide crush energy absorption, and AHSS members outboard of the battery modules prevent intrusion and damage.
The Steel E-Motive body also is engineered for both the rear crash FMVSS and IIHS roof crush requirements. AHSS have enabled these requirements to be comfortably achieved. We will divulge more about these related structures in future blogs.
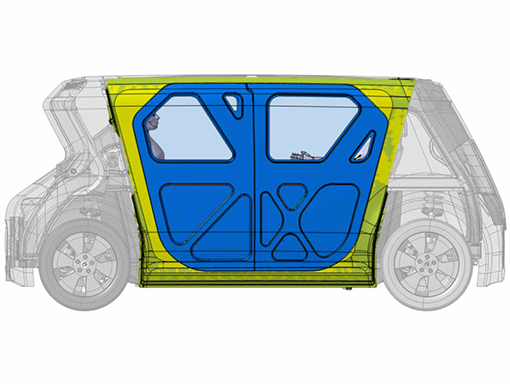
Steel E-Motive’s AHSS A- and C-Pillar placement provide good occupant protection in side pole crash scenarios. The A- and C-Pillar combined with AHSS door ring and door reinforcements compensate for the removed B-Pillar.
Next steps on the Steel E-Motive engineering include in depth structural optimisation through application of the complete portfolio of AHSS grades and manufacturing processes. The objective is to optimise mass and cost, while improving both structural and environmental performance.
Steel E-Motive engineering and validation will be completed in 2022, at which time we will prepare communication and delivery of the final results. But we will be revealing more of the engineering decisions and solutions between now and then as we move towards completion. To stay in touch with webinars, technical publications, and conferences where we will present emerging information, be sure to subscribe.
Learn more about the Steel E-Motive vehicle design.
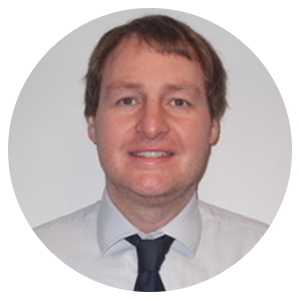
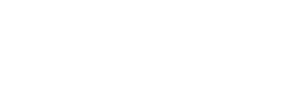
Neil McGregor
Chief Engineer, Steel E-Motive and Ricardo
Subscribe for updates
The Steel E-Motive vehicle concept is still in development. Sign up to be the first to hear about the latest developments from the program.
You might also be interested in